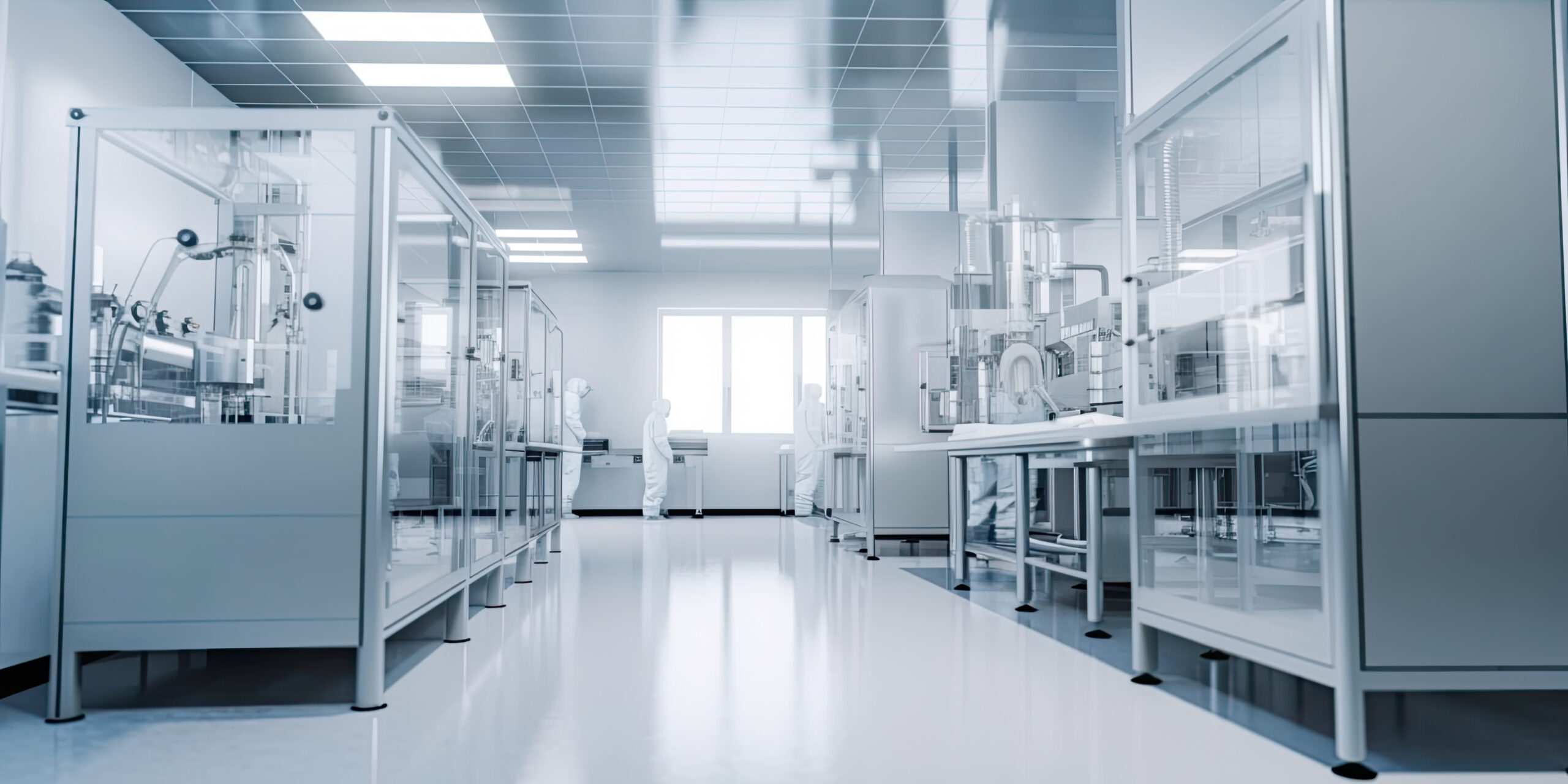
Fields of Application
Cleanrooms
CLEANROOMS
Since 1991, Frigo impianti has specialised in the design and construction of ‘SPECIAL’ systems, one of which is the ‘Clean Room’.
The unique feature of this Special System is that it controls the concentration of particles within the room.
It will be essential to minimise the introduction, generation and retention of polluting particles inside this room. Product contamination due to dust, mould and particles reduces the quality and shelf life of the product itself.
CONTAMINATION IN PRODUCTS
Protecting products from contamination by harmful airborne particles means avoiding contact with dirty air. Itis essential to increase the air quality in the processing room, without forgetting the importance of hygienic conditions, which must be monitored, all for the protection of the products.
FILTERING SYSTEM
Air filtration is practically the most delicate and important process to set up;
The higher the protection of the air by the various filters, the higher the air filtration and purification.
Progressive air filtration prevents filters with a higher protective rating from being damaged and degrading rapidly.
CLEAN ROOM OPERATION
A key feature of clean rooms is that they are often enclosed in small areas that are optimised for production needs. The distribution of air within a cleanroom can be done in different ways and this, together with the various degrees of filtration, determines the effectiveness of protection against product contamination.
VERTICAL filtering is built with filters housed in the ceiling and air intake from the lower parts of the chamber; in this case the clean working area is located in the upper part of the room;
From this classification, we can therefore observe the fundamental role that the choice and positioning of filters play in the design of a clean room.
CLEANROOM FACILITIES
limit the openings between the various controlled atmosphere rooms as much as possible;
entrances and exits must be built with ‘Interlocked Doors’ to minimise contamination and maintain differential pressures between rooms.
AVOIDING CONTAMINATION
The main Contamination comes directly from humans, who are the main vehicle of infection, releasing several million particles of different sizes with just a small movement;
no less important is contamination from production machinery (pneumatic systems with open drains, lubricating oil, condensation drops, drains without sumps, etc.);
production, cleaning, disinfection;
biological contamination through moulds, yeasts and bacteria in the air.
WE CHOOSE THE CLASSIFICATION ACCORDING TOTHE APPLICATION
To choose the application, we must follow Federal Standard 209 E, Federal Standard 290 D and ISO 14644-1, which are referred to for room designations. Furthermore, from Fed.Std.209D it is specified that the conditions under which tests must be carried out to establish environmental contamination classes are:
- unequipped clean room;
- clean room in resting conditions;
- functioning clean room;
ATTENTION TOTHE WORK ENVIRONMENT
small dimensions to ensure a healthy working environment;
positioning of work areas as far as possible from potential sources of contamination;
productive flow from the least sterile to the most sterile room;
elimination/decrease of turbulence within clean rooms;
easy access to all cleanroom areas for cleaning operations;
accessories that comply with international safety and hygiene regulations.
SETTING THE CORRECT PARAMETERS
The fundamental environmental parameters are that series of parameters that must be monitored for product quality, for packaging and waste, for energy consumption, for machine operation and last but not least, for viability by the operating staff. These parameters are:
temperature and humidity: humidity control, in addition to being fundamental for product quality, is of great importance in relation to problems related to corrosion, condensation on work surfaces and reduction of electrostatic charges;
differential pressures: all the chambers must be kept at static pressures that are sufficiently higher than the atmospheric pressure to prevent any kind of contamination; any air expulsion from the chambers must therefore be counterbalanced by new intakes to keep the environmental pressure value unchanged;
lighting: the level of lighting, its uniformity and the colour of the light must be checked;
noise and vibrations: they can be hazardous for both the operating staff and the equipment.
NOT ONLY PURIFICATION BUT ALSO CLEANING
In addition to normal operation as an air conditioning unit, the system also involves the expulsion of humid air, generated during the washing operation of the work environment. The air handling unit will introduce hot air during this phase to facilitate drying of surfaces and equipment.