Our technologies
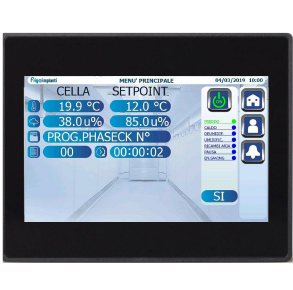
HMI DRYING:
The human machine interface (HMI) consists of 65,000-colour touch-screen panels in 16:9 format and TFT technology.
The multi-machine software, developed by Frigo Impianti’s IT department, is configured to manage the various machine types and in particular:
- Display the status of system operating parameters (plc inputs/outputs, room temperature and humidity reading, gas pressure reading, ventilation inverter status, etc.)
- Set software control parameters (room temperature and humidity setpoints, pause durations, air changes, ventilation speed, etc.)
- Switch the system on/off
- Display and reset any alarms
The panel can also be connected, via Ethernet, to the customer’s company network in order to display, via VNC protocol, the status of the system, as if one were in front of the panel itself.
PLC DRYING:
System operation is provided by a Rockwell (Allen-Bradley) Micro850 family Plc, equipped with a number of additional input-output cards and a communication port that, via an Ethernet switch, allows data to be exchanged with the HMI, inverters and the factory system
The multi-machine software, developed by Frigo Impianti’s IT department, is configured to manage the various machine types and in particular:
- Read the status of temperature, humidity and pressure sensors
- Based on the operator’s settings via the hmi, control the various utilities (refrigeration circuit, hot water circuit, ventilation, etc.)
- Switch the system on/off
- Modify machine behaviour based on process timers or reading sensor drifts
- Receive various alarms from the system and, consequently, interrupt the operation of the relevant utilities
REMOTE CONTROL AND SUPERVISION OF INSTALLATIONS:
This system, which is composed of an in-house developed software and a dedicated device enables the programming and remote control of all “user” parameters and regulation of historical values of: temperature, humidity, alarms of each individual system, for a period of 18 months.
Using a series of detailed screens, all parameters of each individual system can be programmed conveniently and quickly.
Once they have been input, the values are sent to the system controller, who uses them to change processing according to the user’s requests.
According to the system’s controlled characteristics, it is possible to have a “Graphic” view of performance over time of the following sizes:
• Room temperature
• Room humidity
• Air exchange activation
• Energy-saving or Enthalpy activation
Or display, via a table REPORT:
Recordings are memorised on the hard disk of the user PC in order to enable consultation of historical values for a period of 18 months established by the laws in force.
It is, however, possible to make a backup of all data in order to keep information for a longer period of time.
The PC will alert the operator of any alarms generated by the supervised systems, via a messaging app, and will specify:
• Date and time of activation and deactivation
• Description and type of alarm
• Reference to the system involved
By means of a special screen, it is possible to control the status of each individual system immediately.
In addition to the values of the analogical quantities (temperature probe, humidity probe, gas pressure probe, etc.), it is also possible to see the digital values that show the ON/OFF state of all system devices.